Are you properly documenting important quality control tasks?
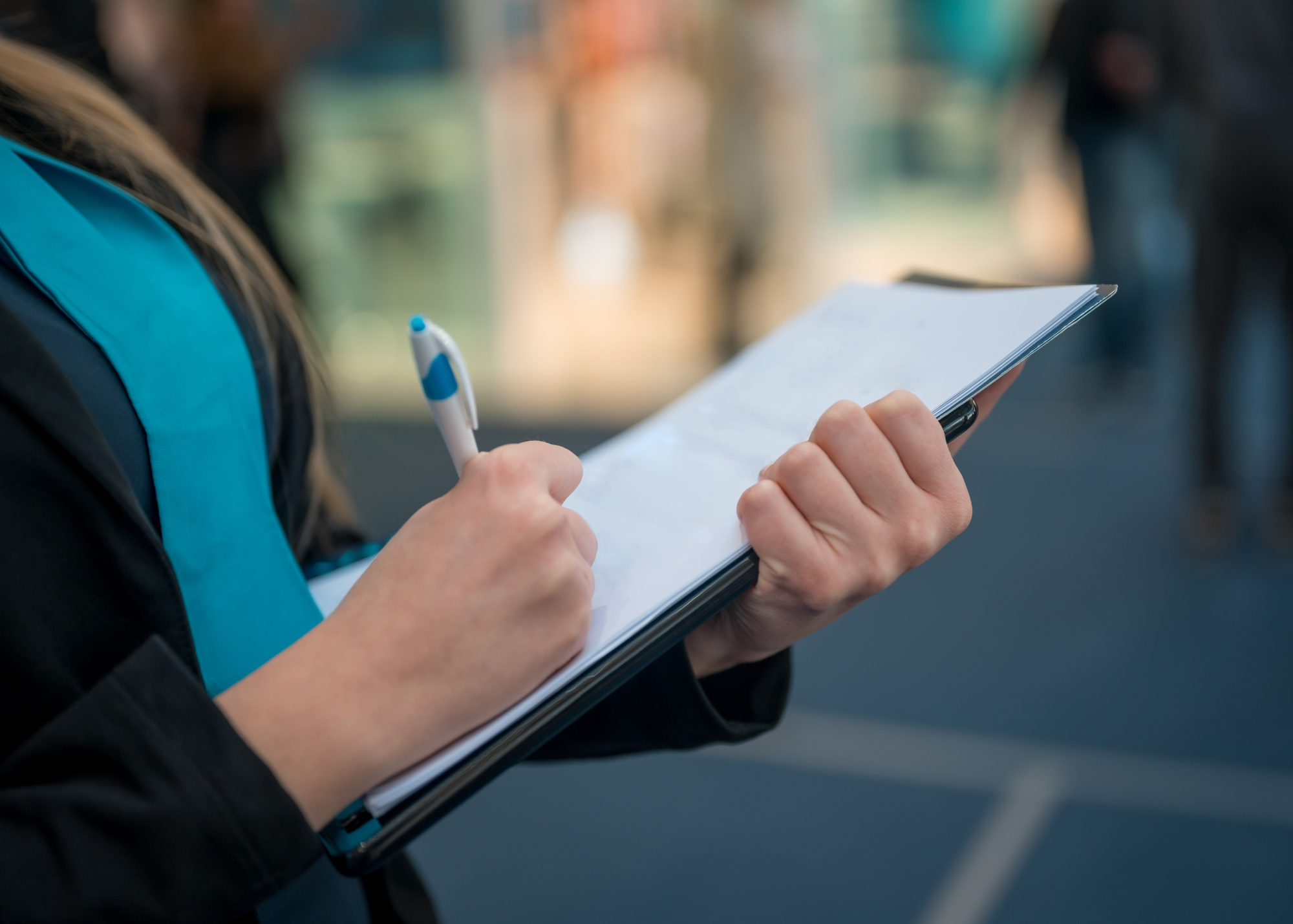
by Terri Walker
During an OSHA or Dental Board inspection or audit, the inspector will likely begin by requesting your documentation, which will include your safety policies and records of completed tasks.
How do you demonstrate compliance? Clearly having written policies and procedures are essential. How do you prove that the required tasks are completed? First, outline the necessary tasks and functions that must be completed and then delegate those duties to a team member. To uphold the highest standards in patient care, infection control, and job safety we must ensure the completion of these functions. This is best accomplished through tasks logs or what we refer to as a Quality Control Program.
Years ago, we provided paper templates to complete. Now we encourage electronic documents particularly for multi-site locations. You can categorize your tasks according to frequency, whether it’s daily, weekly, monthly, periodically and/or yearly.
To launch your quality control program, consider the following important tasks:
- Fire Extinguishers: Document monthly visual inspections and annual professional inspections.
- Weekly Eyewash Station Flush. Document the weekly eyewash station flush and evaluation for proper function.
- Ultrasonic or Instrument Washer. Maintain monthly documentation of the ultrasonic and/or instrument washer test results.
- Sterilization Monitoring. Maintain weekly spore test results and document any corrective action taken if a test fails. Sterilization procedures should be monitored using biological, mechanical, and chemical indicators. Because spore tests are only performed weekly, and the results are usually not obtained immediately, mechanical and chemical monitoring should also be performed to supplement the quality control program. Each instrument package must have an external indicator, an internal integrator, including documentation of the date, time, and load number on each package.
- High-Level Disinfectant: High-level disinfectants (HLD) should only be used for heat-sensitive items. Due to the toxicity of these products, the aim is to minimize their use. If you decide to use an HLD, it is essential to maintain documentation of daily test strip readings to ensure the proper concentration level. Additionally, follow the manufacturer’s instructions for the correct disposal of these products.
- Dental Unit Waterline Monitoring: The Environmental Protection Agency (EPA) regulatory standards for drinking water require that each dental unit waterline maintains bacterial levels below 500 CFU/mL. To comply with regulation, dental practices must keep detailed documentation of waterline testing and maintenance. It is important to document test results and any corrective actions taken in response to failed tests. Monthly testing is required until two consecutive months of passing results are achieved, after which quarterly testing. These records should be maintained for a minimum of five years.
- Biohazardous waste: Facilities must maintain documentation for biohazardous waste, including records of waste generated, treated, and sent off-site. This documentation should consist of manifests, treatment certificates, and logs.
- Pharmaceutical waste: Keep a copy of each manifest, along with exception reports, test results, or waste analyses for a minimum of three years.
- Scrap amalgam: Document the replacement dates of amalgam retaining containers, as well as the dates when collections are picked up or shipped to a licensed disposal facility. This information should be maintained for at least three years.
- Amalgam Separator: Maintain records of monthly inspections and dates when the separator was picked up or shipped to a license disposal facility. This documentation should be maintained for a minimum of three years.
- Hazardous waste: (Glutaraldehyde) disposal: Maintain documentation of mixture and replacement dates, along with daily testing and disposal records for a minimum of 3 years.
- Radiation Reports: Maintain radiation registration and inspection reports according to federal, state, and local regulations.
Conclusion: Enjoy peace of mind by maintaining thorough documentation. If you are interested in MPS assisting you with your quality control program, please contact us at (931) 232-7738 or visit our website at www.modernpracticesolutions.com
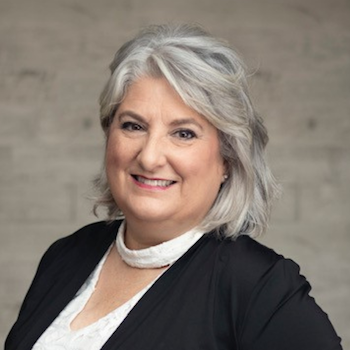